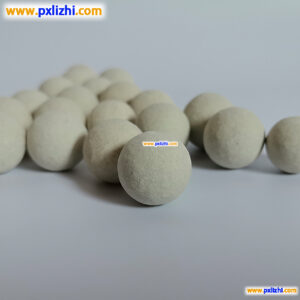
# Ceramic Ball Manufacturing Process and Applications
## Introduction to Ceramic Balls
Ceramic balls are precision-engineered spherical components made from advanced ceramic materials. These balls offer exceptional properties that make them suitable for a wide range of industrial applications. Their unique characteristics include high hardness, wear resistance, corrosion resistance, and thermal stability.
## Manufacturing Process of Ceramic Balls
### 1. Raw Material Selection
The manufacturing process begins with the careful selection of ceramic materials. Common materials used include:
– Alumina (Al2O3)
– Zirconia (ZrO2)
– Silicon Nitride (Si3N4)
– Silicon Carbide (SiC)
### 2. Powder Preparation
The selected ceramic powder is mixed with binders and additives to create a homogeneous mixture. This step ensures:
– Uniform particle size distribution
– Proper flow characteristics
– Consistent density
### 3. Forming Process
Several methods can be used to form ceramic balls:
#### Isostatic Pressing
Cold isostatic pressing (CIP) applies uniform pressure from all directions to create green bodies with high density and minimal defects.
#### Injection Molding
This method is suitable for mass production of small ceramic balls with complex geometries.
#### Extrusion and Spheronization
For larger balls, extrusion followed by spheronization is often employed.
### 4. Sintering
The formed green balls undergo high-temperature sintering to achieve:
– Full densification
– Improved mechanical properties
– Final dimensional accuracy
### 5. Grinding and Polishing
Precision grinding and polishing processes ensure:
– Tight dimensional tolerances
– Excellent surface finish
– Perfect sphericity
### 6. Quality Control
Rigorous quality checks include:
– Dimensional inspection
– Surface quality assessment
– Mechanical property testing
– Roundness measurement
## Applications of Ceramic Balls
### Bearings
Ceramic balls are widely used in high-performance bearings due to their:
– Low density
– High stiffness
– Corrosion resistance
– Electrical insulation properties
### Valve Components
In severe service conditions, ceramic balls provide:
– Excellent wear resistance
– Chemical inertness
– Long service life
### Grinding Media
Ceramic grinding balls offer advantages in milling applications:
– Higher density than steel
– Lower wear rates
Keyword: ceramic ball
– Contamination-free grinding
### Medical Applications
In medical devices, ceramic balls are used for:
– Joint replacements
– Dental implants
– Surgical instruments
### Aerospace and Defense
Specialized applications include:
– Guidance systems
– Gyroscopes
– High-temperature components
## Advantages of Ceramic Balls
Compared to traditional metal balls, ceramic balls offer:
– Higher hardness and wear resistance
– Lower density
– Better corrosion resistance
– Higher temperature capability
– Non-magnetic properties
– Electrical insulation
## Future Trends in Ceramic Ball Technology
The ceramic ball industry continues to evolve with:
– Development of new ceramic compositions
– Improved manufacturing techniques
– Nanostructured materials
– Hybrid ceramic-metal components
– Smart ceramic systems with embedded sensors
## Conclusion
Ceramic balls represent a critical component in many high-performance applications across various industries. Their unique combination of properties makes them indispensable in demanding environments where conventional materials fail. As manufacturing technologies advance, we can expect to see even broader adoption of ceramic balls in new and innovative applications.