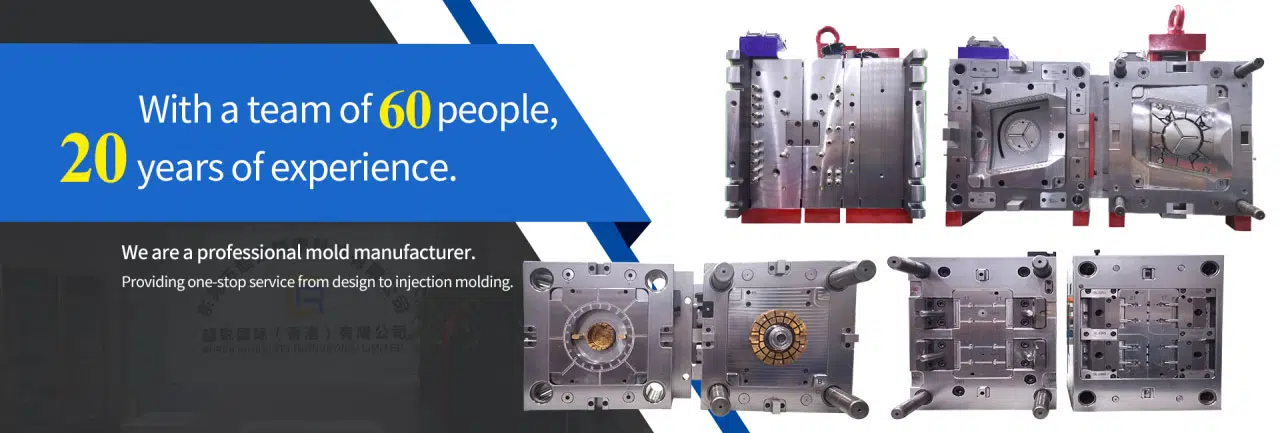
# SKD11 Tool Steel Properties and Applications
## Introduction to SKD11 Tool Steel
SKD11 is a high-carbon, high-chromium tool steel that has gained widespread popularity in the manufacturing industry. This Japanese-grade steel is known for its excellent wear resistance, high hardness, and good dimensional stability after heat treatment. As a cold work tool steel, SKD11 finds applications in various demanding industrial environments.
## Chemical Composition of SKD11
The exceptional properties of SKD11 tool steel stem from its carefully balanced chemical composition:
– Carbon (C): 1.40-1.60%
– Chromium (Cr): 11.00-13.00%
– Molybdenum (Mo): 0.80-1.20%
– Vanadium (V): 0.20-0.50%
– Manganese (Mn): ≤0.60%
– Silicon (Si): ≤0.40%
This composition provides the steel with its characteristic hardness and wear resistance while maintaining sufficient toughness for tooling applications.
## Mechanical Properties of SKD11
SKD11 tool steel exhibits several remarkable mechanical properties:
– Hardness: 58-62 HRC after heat treatment
– Tensile Strength: Approximately 2000 MPa
– Yield Strength: Around 1800 MPa
– Impact Toughness: Good for its hardness level
– Wear Resistance: Excellent due to high chromium content
– Dimensional Stability: Maintains shape well during heat treatment
## Heat Treatment of SKD11
Proper heat treatment is crucial for achieving the optimal properties of SKD11 tool steel:
Keyword: SKD11 Tool Steel
### Annealing
SKD11 is typically supplied in annealed condition with a hardness of about 235 HB. The annealing process involves heating to 820-870°C followed by slow cooling.
### Hardening
For hardening, SKD11 is heated to 1000-1025°C, followed by oil quenching or air cooling. This process achieves maximum hardness.
### Tempering
Tempering is performed at 150-200°C to relieve stresses while maintaining high hardness. Multiple tempering cycles are often recommended for best results.
## Applications of SKD11 Tool Steel
SKD11 finds extensive use in various industrial applications due to its combination of properties:
### Cutting Tools
– Blanking dies
– Trimming dies
– Piercing punches
– Shearing blades
### Forming Tools
– Cold forging dies
– Drawing dies
– Bending tools
– Extrusion tools
### Plastic Molds
– Injection molds
– Compression molds
– Die-casting molds (for non-ferrous metals)
### Other Applications
– Gauges
– Jigs
– Fixtures
– Precision measuring instruments
## Advantages of SKD11 Tool Steel
SKD11 offers several advantages over other tool steels:
– Superior wear resistance for extended tool life
– High compressive strength
– Good machinability in annealed condition
– Excellent polishability
– Relatively good toughness for its hardness level
– Minimal distortion during heat treatment
## Comparison with Similar Tool Steels
While SKD11 shares similarities with other tool steels, it has distinct characteristics:
### SKD11 vs D2
SKD11 is the Japanese equivalent of AISI D2 steel, but with slightly different composition limits. SKD11 typically has better polishability and slightly higher chromium content.
### SKD11 vs SKD61
SKD61 is a hot work tool steel, while SKD11 is a cold work tool steel. SKD11 maintains hardness better at lower temperatures, while SKD61 performs better at elevated temperatures.
## Machining and Fabrication Considerations
When working with SKD11 tool steel, several factors should be considered:
### Machining in Annealed Condition
SKD11 machines relatively well in its annealed state (235 HB). Using proper cutting tools and parameters is essential for efficient machining.
### Gr