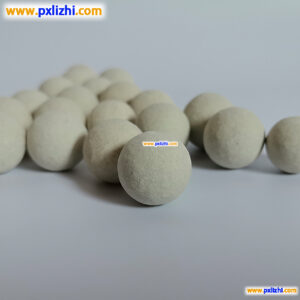
,文章长度约1000单词
html
Ceramic Ball Manufacturing Process and Applications
Ceramic balls are highly versatile components used across various industries due to their exceptional properties such as high hardness, wear resistance, and thermal stability. Understanding their manufacturing process and applications can help in selecting the right type for specific needs.
The Manufacturing Process of Ceramic Balls
The production of ceramic balls involves several precise steps to ensure quality and performance. Here’s an overview of the typical manufacturing process:
1. Raw Material Selection
The process begins with selecting high-purity ceramic materials such as alumina (Al2O3), zirconia (ZrO2), or silicon nitride (Si3N4). The choice depends on the desired properties of the final product.
2. Powder Preparation
The selected ceramic powder is mixed with binders and additives to improve formability. This mixture is then milled to achieve a uniform particle size distribution, which is crucial for consistent quality.
3. Forming
The powder mixture is shaped into spherical forms using various methods:
- Dry Pressing: Powder is compressed in a mold under high pressure.
- Isostatic Pressing: Powder is subjected to uniform pressure from all directions using a liquid medium.
- Injection Molding: Powder-binder mixture is injected into molds under high pressure.
4. Sintering
The formed balls are heated in a kiln at temperatures between 1400°C to 1800°C, depending on the material. This process densifies the ceramic, eliminating porosity and enhancing mechanical properties.
5. Grinding and Lapping
After sintering, the balls undergo precision grinding and lapping to achieve exact dimensions and surface finish. This step is critical for applications requiring high precision.
6. Quality Control
Each batch undergoes rigorous testing for dimensional accuracy, surface quality, and mechanical properties like hardness and fracture toughness.
Applications of Ceramic Balls
Ceramic balls find use in numerous industries due to their superior performance characteristics:
1. Bearings
Ceramic balls are widely used in high-performance bearings for applications requiring:
- High-speed operation
- Corrosion resistance
- Electrical insulation
- Reduced weight
They’re particularly valuable in aerospace, medical, and semiconductor equipment.
2. Valves and Pumps
In fluid handling systems, ceramic balls serve as:
- Check valve components
- Pump bearings
- Flow control elements
Their chemical inertness makes them ideal for corrosive or high-purity applications.
3. Grinding Media
Ceramic balls are excellent grinding media for:
- Paint and pigment production
- Pharmaceutical processing
- Food industry applications
They offer contamination-free grinding with minimal wear.
4. Automotive Industry
Keyword: ceramic ball
Modern vehicles utilize ceramic balls in:
- Turbocharger bearings
- Fuel