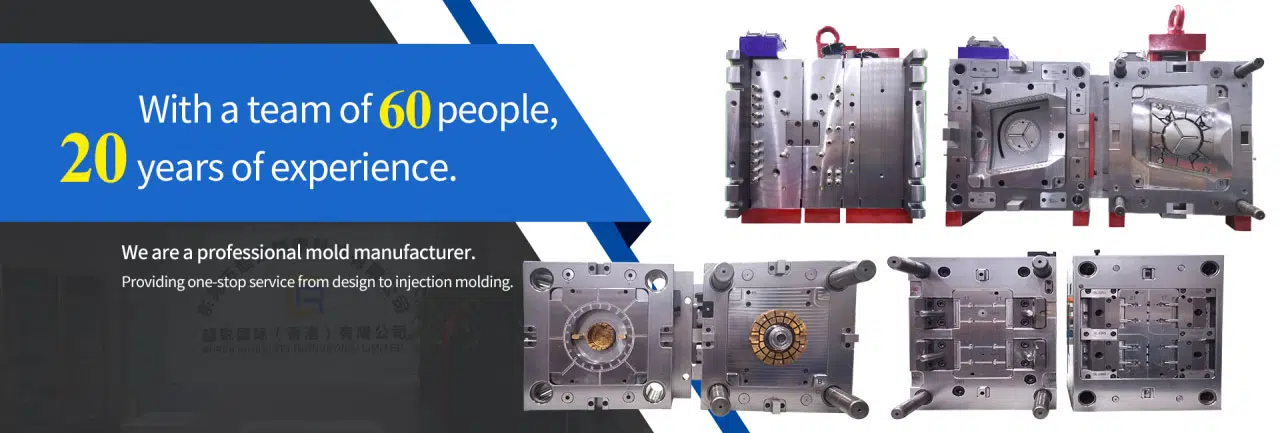
# High-Precision Machining Techniques and Applications
## Introduction to High-Precision Machining
High-precision machining refers to manufacturing processes that achieve extremely tight tolerances and superior surface finishes. This specialized form of machining has become increasingly important in industries where component accuracy is critical to performance and reliability.
## Key Techniques in High-Precision Machining
### 1. Micro-Machining
Micro-machining involves creating extremely small features with dimensions typically measured in micrometers. This technique is essential for producing components used in medical devices, electronics, and aerospace applications.
### 2. Ultra-Precision Turning
Using specialized lathes with nanometer-level positioning accuracy, ultra-precision turning can produce parts with surface finishes as smooth as 1 nanometer Ra. This process is particularly valuable for optical components and precision bearings.
Keyword: High-Precision Machining
### 3. High-Speed Machining (HSM)
HSM combines high spindle speeds with advanced toolpath strategies to achieve both precision and productivity. The technique minimizes heat generation and tool deflection, resulting in better dimensional accuracy.
## Materials for High-Precision Machining
High-precision machining works with a variety of materials, each presenting unique challenges:
- Metals: Titanium, aluminum, stainless steel, and specialty alloys
- Plastics: PEEK, Ultem, and other engineering-grade polymers
- Ceramics: Advanced technical ceramics for extreme environments
- Composites: Carbon fiber and other reinforced materials
## Applications Across Industries
Medical Device Manufacturing
The medical industry relies heavily on high-precision machining for implants, surgical instruments, and diagnostic equipment where micron-level accuracy can impact patient outcomes.
Aerospace and Defense
Critical aircraft components, guidance systems, and satellite parts demand the highest levels of precision to ensure safety and performance in extreme conditions.
Automotive Engineering
From fuel injection systems to transmission components, high-precision machining enables the production of parts that improve vehicle efficiency and reliability.
Electronics and Semiconductor
The miniaturization trend in electronics requires machining capabilities that can produce microscopic features with exceptional consistency.
## Future Trends in High-Precision Machining
The field continues to evolve with several emerging trends:
- Integration of AI and machine learning for predictive maintenance and process optimization
- Development of hybrid manufacturing systems combining additive and subtractive processes
- Advancements in metrology for real-time quality control
- Increased use of automation for 24/7 precision manufacturing
## Conclusion
High-precision machining remains at the forefront of manufacturing innovation, enabling the production of components that push the boundaries of technology across multiple industries. As tolerances continue to tighten and materials become more challenging, the techniques and equipment used in high-precision machining will continue to advance to meet these demanding requirements.