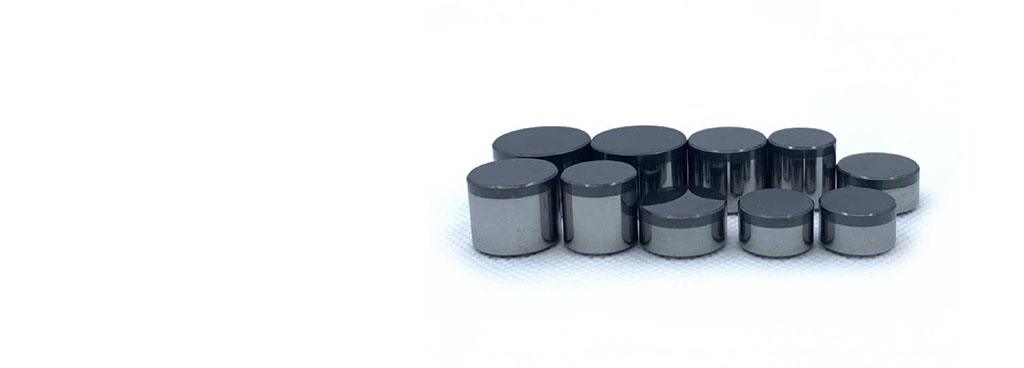
# PDC Cutter Manufacturing Facility: The Heart of Cutting-Edge Drilling Technology
## Introduction to PDC Cutter Production
Polycrystalline Diamond Compact (PDC) cutters have revolutionized the drilling industry with their exceptional durability and cutting efficiency. At the core of this technological advancement lies the PDC cutter factory, where precision engineering meets innovative material science to create these remarkable cutting tools.
## The Manufacturing Process
### Raw Material Selection
Every high-quality PDC cutter begins with carefully selected raw materials. The manufacturing facility sources premium-grade synthetic diamond powder and tungsten carbide substrates, ensuring the foundation for superior cutter performance.
### High-Pressure, High-Temperature (HPHT) Synthesis
The PDC cutter factory employs state-of-the-art HPHT presses to bond the diamond layer to the carbide substrate. This process, conducted at pressures exceeding 50,000 atmospheres and temperatures around 1,500°C, creates the ultra-hard polycrystalline diamond table that gives PDC cutters their remarkable wear resistance.
### Precision Machining and Quality Control
After synthesis, each cutter undergoes meticulous machining to achieve precise geometries. Advanced CNC grinding machines create the optimal cutting profiles while maintaining tight tolerances. The facility implements rigorous quality control measures, including:
– Non-destructive testing
– Microstructure analysis
– Performance benchmarking
– Dimensional verification
## Advanced Features of Modern PDC Cutter Factories
### Automated Production Lines
Leading PDC cutter manufacturing facilities have embraced automation to enhance consistency and productivity. Robotic systems handle material transfer, press loading, and quality inspection, minimizing human error while maximizing output.
### Research and Development Centers
Innovation is continuous in top-tier PDC cutter factories. Dedicated R&D departments focus on:
– Developing new diamond formulations
– Optimizing interface designs
– Improving thermal stability
– Enhancing impact resistance
### Environmental Considerations
Modern PDC cutter manufacturing facilities prioritize sustainability through:
– Energy-efficient HPHT presses
– Closed-loop cooling systems
– Material recycling programs
– Waste reduction initiatives
## Applications of Factory-Produced PDC Cutters
The output from a PDC cutter factory serves multiple industries:
– Oil and gas drilling bits
– Mining tools
– Geothermal drilling equipment
– Construction and trenching tools
– Specialized cutting applications
## The Future of PDC Cutter Manufacturing
As drilling challenges become more complex, PDC cutter factories continue to innovate. Emerging trends include:
Keyword: pdc cutter factory
– Nano-structured diamond composites
– Functionally graded interfaces
– Smart cutter designs with embedded sensors
– Additive manufacturing techniques
The PDC cutter manufacturing facility remains at the forefront of drilling technology, constantly pushing the boundaries of what’s possible in cutting tool performance and reliability.