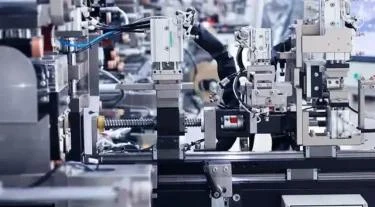
# Tape Production Techniques and Innovations
## The Evolution of Tape Manufacturing
Tape manufacturing has come a long way since its humble beginnings in the early 20th century. What started as simple adhesive strips has evolved into a sophisticated industry producing specialized tapes for countless applications. Modern tape production combines advanced materials science with precision engineering to create products that meet increasingly demanding performance requirements.
## Core Tape Production Techniques
### 1. Coating Methods
The foundation of tape manufacturing lies in the coating process. Three primary techniques dominate the industry:
– Direct coating: Where adhesive is applied directly to the backing material
– Transfer coating: Where adhesive is first applied to a release liner before being transferred to the backing
– Hot melt coating: Where thermoplastic adhesives are applied in molten form
### 2. Drying and Curing
After coating, tapes undergo careful drying or curing processes. Solvent-based adhesives require extensive drying ovens, while UV-curable adhesives use specialized light systems. The choice depends on the adhesive chemistry and desired tape properties.
### 3. Slitting and Rewinding
Precision slitting transforms wide rolls of coated material into finished tape widths. Modern slitting equipment can achieve tolerances within ±0.1 mm, with some specialty tapes requiring even greater precision.
## Innovative Advancements in Tape Production
### Nanotechnology Applications
Recent breakthroughs have incorporated nanomaterials into tape manufacturing:
– Carbon nanotube-infused adhesives for enhanced conductivity
– Nano-silica particles for improved thermal resistance
– Graphene coatings for ultra-thin conductive tapes
### Smart Tape Technologies
The industry is seeing growing interest in functional tapes with advanced capabilities:
– Pressure-sensitive tapes that change color to indicate proper application
– Self-healing adhesives that repair minor surface damage
– Temperature-responsive tapes with adjustable adhesion properties
### Sustainable Manufacturing Practices
Environmental concerns are driving innovation in green production methods:
– Water-based adhesives replacing solvent-based systems
– Biodegradable backing materials from plant-based polymers
– Closed-loop solvent recovery systems in coating operations
## Quality Control in Modern Tape Production
Contemporary tape manufacturing employs sophisticated quality assurance measures:
– Real-time thickness monitoring using laser micrometers
– Automated adhesion testing at production line speeds
– Spectral analysis for consistent chemical composition
– High-speed vision systems for defect detection
## Future Trends in Tape Manufacturing
The tape industry continues to evolve with several promising developments:
– 3D printable adhesive systems for customized applications
– Bio-inspired adhesives mimicking gecko foot structures
– Energy-harvesting tapes that generate power from mechanical stress
– AI-optimized production lines for predictive quality control
As tape manufacturing techniques advance, we can expect to see even more innovative products that push the boundaries of what adhesive tapes can achieve in industries ranging from electronics to aerospace to medical applications.
Keyword: tape manufacturing