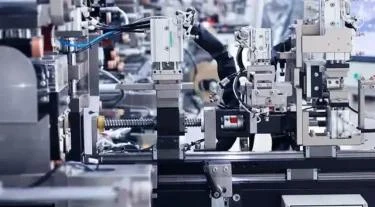
# Tape Manufacturing Process and Techniques
## Introduction to Tape Manufacturing
Tape manufacturing is a complex process that involves multiple stages to produce various types of adhesive tapes for different applications. From everyday household uses to industrial applications, tapes serve numerous purposes across various industries. The manufacturing process combines material science, chemical engineering, and precision machinery to create products with specific adhesive properties and physical characteristics.
## Raw Materials in Tape Production
The foundation of tape manufacturing lies in selecting the right raw materials. The primary components include:
– Backing material (film, paper, cloth, or foil)
– Adhesive (rubber-based, acrylic, or silicone)
– Release liner (for some tape types)
– Additives (tackifiers, stabilizers, and fillers)
Each material is carefully chosen based on the intended application of the final product, whether it needs to withstand extreme temperatures, resist chemicals, or provide temporary or permanent bonding.
## The Tape Manufacturing Process
### 1. Backing Material Preparation
The process begins with preparing the backing material, which serves as the foundation of the tape. Depending on the type of tape being produced, this could involve:
– Extruding plastic films
– Weaving or treating fabric
– Processing paper or foil materials
– Coating materials with special treatments
### 2. Adhesive Formulation and Application
The adhesive formulation is crucial to the tape’s performance. This stage involves:
– Mixing base polymers with tackifiers and additives
– Preparing solvent-based or water-based adhesive solutions
– Applying the adhesive to the backing material using various coating techniques:
– Knife-over-roll coating
– Reverse roll coating
– Slot die coating
– Gravure coating
### 3. Drying and Curing
After adhesive application, the coated material goes through drying ovens to:
– Remove solvents or water
– Cure the adhesive to achieve optimal properties
– Ensure proper cross-linking of polymer chains
### 4. Slitting and Rewinding
The large rolls of coated material are then processed through precision slitting machines to:
– Cut the material into desired widths
– Rewind onto smaller cores
– Package for shipping or further processing
## Specialized Tape Manufacturing Techniques
### Pressure-Sensitive Tape Production
Pressure-sensitive tapes represent the majority of tape products. Their manufacturing requires:
– Precise control of adhesive thickness
– Careful selection of release coatings
– Controlled winding tension to prevent blocking
### Double-Sided Tape Manufacturing
Double-sided tapes require additional steps:
– Application of adhesive to both sides
– Use of release liners during processing
– Special winding techniques to prevent adhesion during storage
### Specialty Tape Production
Special applications demand unique manufacturing approaches:
– High-temperature tapes require heat-resistant materials
– Medical tapes need biocompatible adhesives
– Electrical tapes must have specific dielectric properties
## Quality Control in Tape Manufacturing
Maintaining consistent quality is paramount in tape production. Manufacturers implement:
– Regular viscosity testing of adhesives
– Peel strength measurements
– Shear resistance testing
– Visual inspections for defects
– Environmental testing for specific applications
## Environmental Considerations
Modern tape manufacturing focuses on sustainability through:
– Reduction of solvent use
– Development of water-based adhesives
– Recycling programs for production waste
– Energy-efficient drying systems
– Use of biodegradable materials where possible
## Future Trends in Tape Manufacturing
The industry continues to evolve with:
– Nanotechnology in adhesive formulations
– Smart tapes with embedded sensors
– Bio-based adhesive development
– Advanced coating technologies for precision application
– Automated quality control systems
The tape manufacturing process combines scientific precision with industrial scale production to create products that are both simple in concept and complex in execution. As technology advances, tape manufacturers continue to innovate, developing new products to meet the ever-changing demands of modern industry and consumers.
Keyword: tape manufacturing