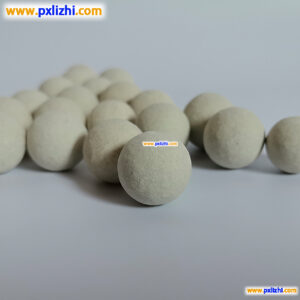
# Ceramic Ball Manufacturing Process and Applications
## Introduction to Ceramic Balls
Ceramic balls are high-performance spherical components made from advanced ceramic materials. These precision-engineered balls offer exceptional properties that make them ideal for various industrial applications. Their unique characteristics stem from the manufacturing process and the ceramic materials used in their production.
## The Manufacturing Process of Ceramic Balls
Keyword: ceramic ball
### 1. Raw Material Selection
The production of ceramic balls begins with the careful selection of raw materials. Common ceramic materials used include:
– Alumina (Al2O3)
– Zirconia (ZrO2)
– Silicon nitride (Si3N4)
– Silicon carbide (SiC)
### 2. Powder Preparation
The selected ceramic powder undergoes several preparation steps:
– Milling to achieve uniform particle size
– Mixing with binders and additives
– Spray drying to create free-flowing granules
### 3. Forming Process
There are several methods to form ceramic balls:
– Isostatic pressing: Uses hydraulic pressure to form spherical shapes
– Extrusion: Forms cylindrical shapes that are later rounded
– Injection molding: Suitable for complex shapes and high-volume production
### 4. Sintering
The formed balls undergo high-temperature sintering:
– Temperatures typically range from 1400°C to 1800°C
– Process duration varies from several hours to days
– Results in dense, strong ceramic microstructure
### 5. Precision Grinding and Polishing
After sintering, the balls undergo precision finishing:
– Diamond grinding to achieve exact dimensions
– Lapping for superior surface finish
– Polishing to nanometer-level smoothness
### 6. Quality Control
Each ceramic ball undergoes rigorous testing:
– Dimensional accuracy checks
– Surface finish measurements
– Mechanical property testing
– Visual inspection for defects
## Applications of Ceramic Balls
### 1. Bearing Applications
Ceramic balls are widely used in high-performance bearings:
– Hybrid bearings (ceramic balls with steel races)
– Full ceramic bearings
– Applications in aerospace, medical, and high-speed machinery
### 2. Valve Components
Their excellent wear resistance makes them ideal for:
– Check valves
– Ball valves
– Flow control valves
### 3. Grinding Media
Ceramic balls serve as grinding media in:
– Paint and pigment industries
– Pharmaceutical production
– Food processing
### 4. Automotive Applications
Used in various automotive components:
– Fuel injection systems
– Turbochargers
– High-performance engines
### 5. Medical Applications
Biocompatible ceramic balls are used in:
– Orthopedic implants
– Dental applications
– Surgical instruments
## Advantages of Ceramic Balls
Ceramic balls offer numerous benefits over traditional metal balls:
– High hardness and wear resistance
– Excellent corrosion resistance
– Lightweight (about 40% lighter than steel)
– High-temperature stability
– Electrical insulation properties
– Non-magnetic characteristics
## Future Trends in Ceramic Ball Technology
The ceramic ball industry continues to evolve with:
– Development of new ceramic composites
– Improved manufacturing techniques for higher precision
– Expansion into new application areas
– Cost reduction through optimized production processes
As technology advances, ceramic balls are expected to play an increasingly important role in various high-tech industries, offering solutions where traditional materials reach their performance limits.